デジタル化すれば、事務作業から解放されてプレス金型設計や製作に集中できる
公開日:
2022年3月18日(金)
閲覧数:162 回
群馬県は、昔から繊維や木工、食品などの製造業が盛んです。今、県内の生産額で最も多いのが、自動車などの「輸送用機械器具製造業」です。特に群馬県太田市は、スバルが拠点を置く「スバル町(旧・東本町)」で有名でもあります。そんな群馬県内には、自動車メーカーを支える、優れた技術を持つ金属加工業などの中小製造業が数多くあります。
群馬県IoTラボ(群馬県IoT・AI推進研究会)は、群馬産業技術センターなどの支援機関が中心となって、中小製造業だけでは対応が困難なIoTおよびAI技術の導入・活用をサポートする産学官連携組織です。「技術の高度化、生産性の向上などを図ること」を目的とし、公設試験研究機関、大学や高専、産業支援機関らが連携して情報提供や人材育成等の各種事業を実施しています。
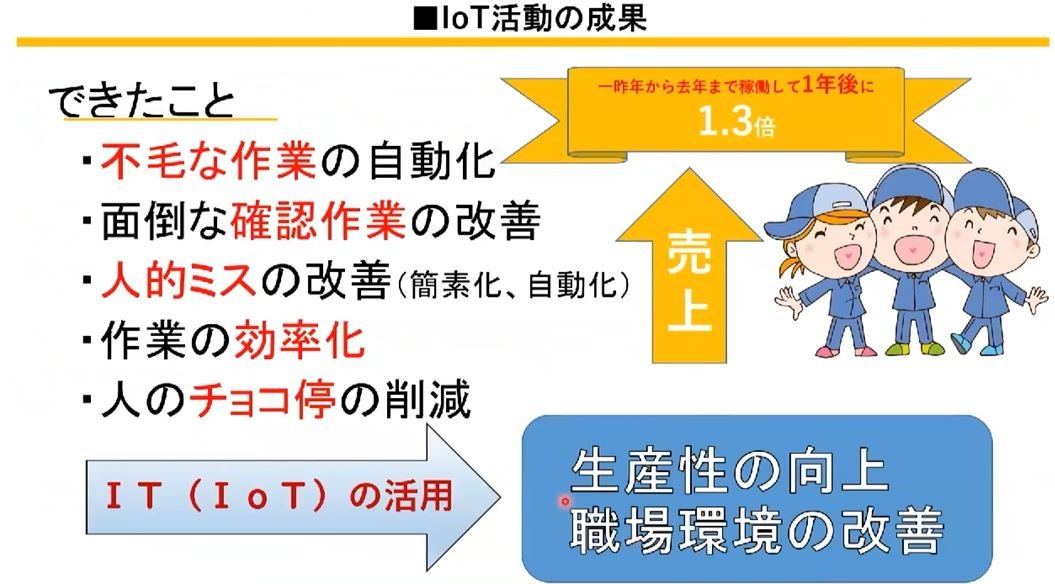
鈴木工業さんでは従来、それぞれの工程に担当が付いており、自分以外の担当者が「いつ、どの設備を使用して加工しているか、どういう状況にあるか」などを頻繁な電話確認を行う必要がありました。
この課題を解消するためにはタイムリーに状況を把握する必要があり、その手段として考えたのがQRコードを用いた加工の進捗管理のデジタル化です。
最初に取り組んだのが、顧客ごとに作成していた部品表の社内標準化です。このことにより、個々の部品に対してQRコードを発行することができ、それをシールにして部品に貼り付け管理する仕組みを作りました。各加工が終わるごとにQRコードを読み取ることで、どの部品がどの場所にあり、どこまで進んでいるかの情報が集約できるようになったのです。このデータを社内サーバに収集し、納期情報と比較することで、進捗度や予定に対して遅れている原因が一目でわかるシステムを開発し、導入しました。
現在社内の4カ所で確認でき、それぞれの工程状況をいつでも誰でも確認可能になりました。このことにより、従来行っていた関連部署への進捗確認の電話連絡は一切なくなりました。
この他、加工データ作成の自動化による人為的ミスの削減等、さまざまな業務をデジタル化し、仕事の高効率化を図った結果、「社員30人中2人分の仕事を削減」することができ、経済的効果が確認できたといいます。それにより本来取り組むべき金型の新しい加工技術構築のための時間に費やすことができるようになったということです。
「例えば、事務担当であるが現場業務の一部も手伝っていたような人が、事務作業から解放されることで、CADやCAEなど新しいスキルを習得する時間に当てられるようになり、スキルアップが図れています」と、群馬産業技術センターの高橋氏は言います。
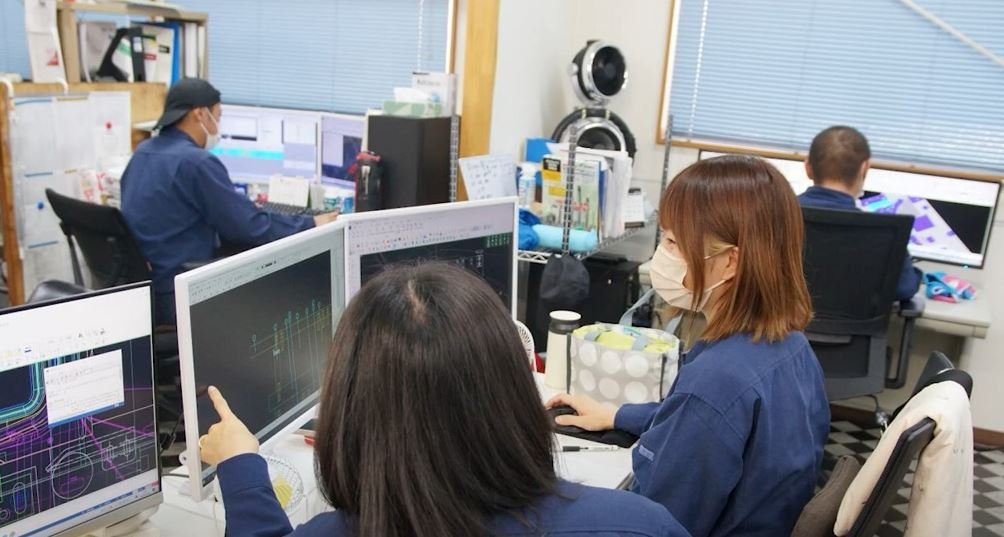
そこで、先進的なデジタル化の取り組み事例を目の当たりにしたことが、「自社はなぜ、それができないのだろうか」と考える大きなきっかけとなり、デジタル化を強く進めようと決意されたということです。
デジタル化をすることによる業務効率化の効果は、定量的な評価がなかなか難しいものです。このプロジェクトでもそうであり、現場の理解を得るために時間がかなりかかったといいます。「ITに馴染みのない現場の技術者さんの理解を得るために苦労しました。QRコードについても、なんとなくは知っていても、『それを仕事に使ってどうなるのか、ピンとこない』という状態でした」と、高橋氏は振り返ります。
そこで、数字により示すより、「自ら、体感してもらう」作戦を取ることに。デジタル技術の中で業務をしてもらうことで、間接業務から解放され、人為的ミスもなくなり、作業効率が高まったことを実感してもらうことが理解へつながっていったといいます。
鈴木翔太社長は「面倒な事務仕事が減り、余裕が生まれた社員が本業である金型加工技術の向上に目を向けてくれました。単なる自動化ではなく、人の成長が生産性革新を生んだのではないでしょうか。」とおっしゃっています。
また、群馬県IoTラボとしては、中小企業が抱える困りごとを解決するため、現場に赴いて、社内の現場の人から話をじっくりと聞き、自分自身が社員になったつもりでプロジェクトに取り組んだそうです。
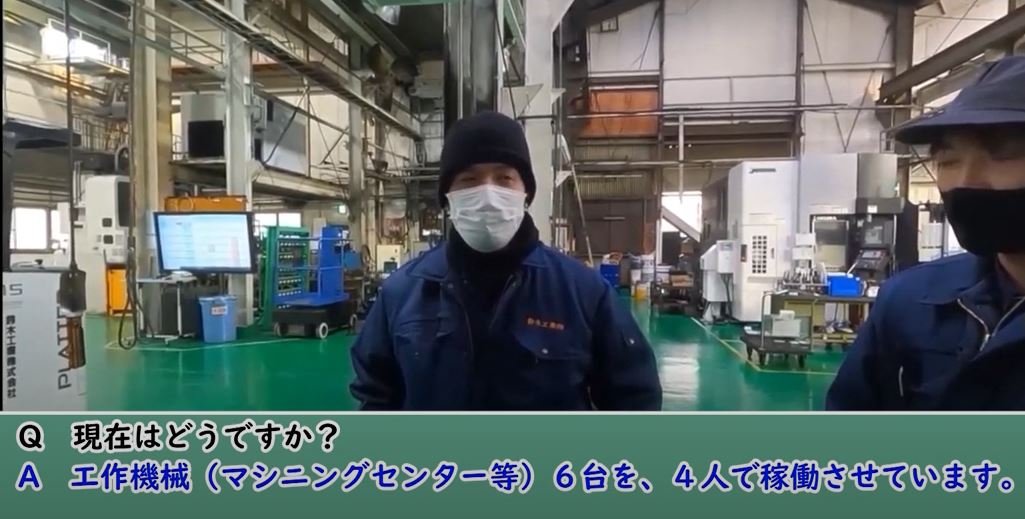
鈴木工業さんは、「社内のデジタル化は全業務の8割程度まで実現できているが、今後も継続してデジタル技術を取り入れ、生産性革新を目指していく」ということです。
群馬県IoTラボ(群馬県IoT・AI推進研究会)は、群馬産業技術センターなどの支援機関が中心となって、中小製造業だけでは対応が困難なIoTおよびAI技術の導入・活用をサポートする産学官連携組織です。「技術の高度化、生産性の向上などを図ること」を目的とし、公設試験研究機関、大学や高専、産業支援機関らが連携して情報提供や人材育成等の各種事業を実施しています。
デジタル化により大幅な生産性向上を実現
群馬県IoTラボでは、太田市の鈴木工業株式会社において、自動車用プレス金型工程のデジタル化に取り組み、成功しています。鈴木工業さんのプレス金型製作は、型設計から型加工、部品組み付けまで複数の工程で行われます。それぞれの工程における状況をデジタルで見える化し、主に各担当の進捗報告や事務作業を大幅に減らし、生産効率アップを図ったということです。IoT活動の成果
鈴木工業さんでは従来、それぞれの工程に担当が付いており、自分以外の担当者が「いつ、どの設備を使用して加工しているか、どういう状況にあるか」などを頻繁な電話確認を行う必要がありました。
この課題を解消するためにはタイムリーに状況を把握する必要があり、その手段として考えたのがQRコードを用いた加工の進捗管理のデジタル化です。
最初に取り組んだのが、顧客ごとに作成していた部品表の社内標準化です。このことにより、個々の部品に対してQRコードを発行することができ、それをシールにして部品に貼り付け管理する仕組みを作りました。各加工が終わるごとにQRコードを読み取ることで、どの部品がどの場所にあり、どこまで進んでいるかの情報が集約できるようになったのです。このデータを社内サーバに収集し、納期情報と比較することで、進捗度や予定に対して遅れている原因が一目でわかるシステムを開発し、導入しました。
現在社内の4カ所で確認でき、それぞれの工程状況をいつでも誰でも確認可能になりました。このことにより、従来行っていた関連部署への進捗確認の電話連絡は一切なくなりました。
この他、加工データ作成の自動化による人為的ミスの削減等、さまざまな業務をデジタル化し、仕事の高効率化を図った結果、「社員30人中2人分の仕事を削減」することができ、経済的効果が確認できたといいます。それにより本来取り組むべき金型の新しい加工技術構築のための時間に費やすことができるようになったということです。
「例えば、事務担当であるが現場業務の一部も手伝っていたような人が、事務作業から解放されることで、CADやCAEなど新しいスキルを習得する時間に当てられるようになり、スキルアップが図れています」と、群馬産業技術センターの高橋氏は言います。
設計の様子
デジタル化のメリットを、現場の皆に理解してもらうためには?
鈴木工業さんは以前からコンピュータによるプレス加工シミュレーション等のデジタル技術を競合他社に先駆けて導入していましたが、さらにデジタル化の取り組みを進めようと思ったきっかけは、「2018年に群馬県が主催した先進企業の見学会にデジタル化の推進責任者である鈴木修一さんが参加したこと」であったと黒岩氏は述べています。そこで、先進的なデジタル化の取り組み事例を目の当たりにしたことが、「自社はなぜ、それができないのだろうか」と考える大きなきっかけとなり、デジタル化を強く進めようと決意されたということです。
デジタル化をすることによる業務効率化の効果は、定量的な評価がなかなか難しいものです。このプロジェクトでもそうであり、現場の理解を得るために時間がかなりかかったといいます。「ITに馴染みのない現場の技術者さんの理解を得るために苦労しました。QRコードについても、なんとなくは知っていても、『それを仕事に使ってどうなるのか、ピンとこない』という状態でした」と、高橋氏は振り返ります。
そこで、数字により示すより、「自ら、体感してもらう」作戦を取ることに。デジタル技術の中で業務をしてもらうことで、間接業務から解放され、人為的ミスもなくなり、作業効率が高まったことを実感してもらうことが理解へつながっていったといいます。
鈴木翔太社長は「面倒な事務仕事が減り、余裕が生まれた社員が本業である金型加工技術の向上に目を向けてくれました。単なる自動化ではなく、人の成長が生産性革新を生んだのではないでしょうか。」とおっしゃっています。
また、群馬県IoTラボとしては、中小企業が抱える困りごとを解決するため、現場に赴いて、社内の現場の人から話をじっくりと聞き、自分自身が社員になったつもりでプロジェクトに取り組んだそうです。
現場の声
鈴木工業さんは、「社内のデジタル化は全業務の8割程度まで実現できているが、今後も継続してデジタル技術を取り入れ、生産性革新を目指していく」ということです。